Saturday 12th October saw the Guild meeting at Strathpeffer Community Centre during which an intrepid group of seven braved the mind-swirling, eye-boggling, number-crunching world of braid weaving under the masterful guiding hand and brain of Alison Roddam. Alison began by demonstrating on a number of pre-warped looms with works in progress, to take us steadily through the pattern pick-up aspects of the process, and gave us all chance to try various braid patterns and ‘get our hands in’ with practice before embarking on our own projects.
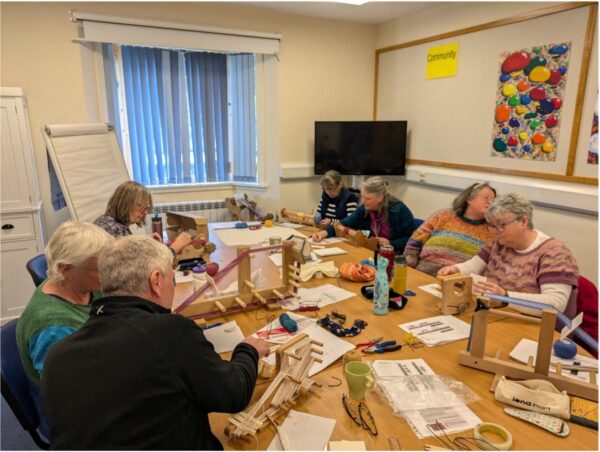
Following this, we selected our own warp and weft yarns from the great selection Alison had brought along, and spent the remaining time before lunch warping our own looms – inkle, inklets and rigid heddles. Warping is usually a bit of a drag, but the size of the braid samples meant it was relatively swift and straightforward, and most of us didn’t need much more than a few minutes to touch base with others, pay our membership fees (!), and grab a quick bite and breath of fresh air before we were back and keen to begin our own patterns.
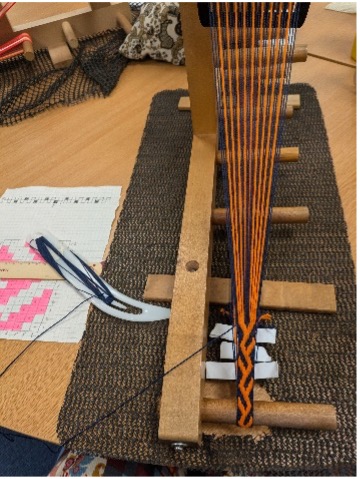
Having been given copies of a selection of Baltic braids by Alison, we were able to choose and copy out our own versions onto the squared paper. Getting our heads around dots and colours was the key to success!
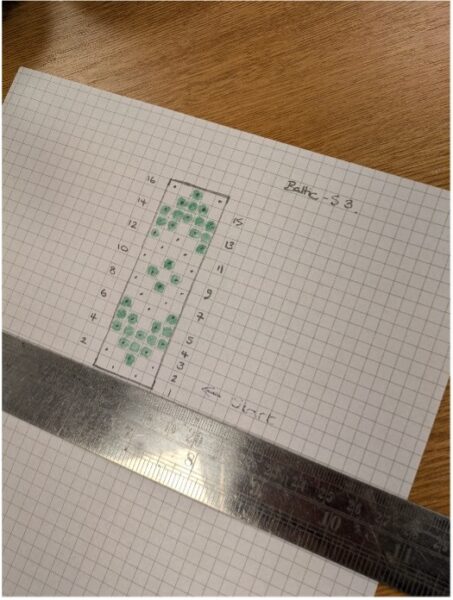
After this we all got into our strides, though not always without hiccoughs along the way. Alison was on hand to guide and advise us throughout and while we varied in speed of working we all left with something established on our looms, a better understanding of the process and an enthusiasm to continue.
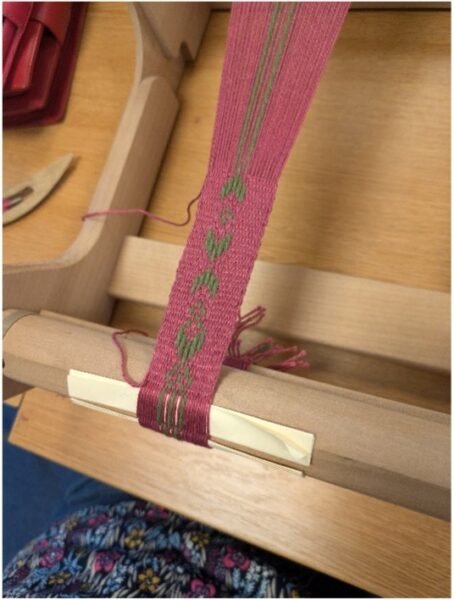
Report by Bex Lockyer